Comprehensive Packaging Machine Repair Service for Quick and Effective Fixes
Comprehensive Packaging Machine Repair Service for Quick and Effective Fixes
Blog Article
Comprehending the Key Elements and Repair Techniques for Product Packaging Machine Upkeep
Effective upkeep of product packaging makers pivots on a complete understanding of their vital elements, including the structure, drive system, and sealing devices. Identifying typical upkeep problems, coupled with the application of preventative techniques and troubleshooting methods, can substantially enhance equipment reliability. The selection of repair work techniques, consisting of the usage of OEM parts and the relevance of certified professionals, plays an important duty in minimizing downtime. To genuinely grasp the intricacies of these systems and their upkeep, one should think about the wider effects of neglecting these crucial practices.
Secret Elements of Packaging Makers
Product packaging makers contain several essential elements that collaborate to ensure efficient and effective packaging processes. At the core of these machines is the frame, which provides architectural honesty and houses the numerous operating parts. The drive system, frequently a mix of equipments and electric motors, facilitates the movement of elements, allowing specific operation throughout the product packaging cycle.
One more crucial part is the conveyor system, which moves items with different stages of the product packaging procedure. This is frequently complemented by sensors and controls that monitor the position and speed of products, making sure synchronization and minimizing errors. The filling up system is critical for properly giving the ideal quantity of product into plans, whether in liquid, powder, or solid kind.
Securing mechanisms, consisting of warmth sealers or sticky applicators, play an important role in safeguarding bundles, stopping contamination and prolonging shelf life. Additionally, labeling systems are indispensable for offering necessary item details, making certain conformity with policies. The control panel, furnished with easy to use user interfaces, allows drivers to take care of machine features, screen efficiency, and make changes as needed, making sure optimal efficiency and performance in product packaging operations.
Usual Maintenance Problems
Reliable procedure of product packaging equipments depends greatly on routine upkeep to stop typical problems that can interrupt production. Among these issues, mechanical deterioration prevails, specifically in components like conveyors, electric motors, and seals, which can cause unexpected downtimes. Additionally, imbalance of components can cause inefficient procedure, triggering products to be incorrectly packaged or damaged throughout the procedure.
An additional typical maintenance issue involves the buildup of dirt and particles, which can hinder the machine's sensing units and relocating components. packaging machine repair service. This not only impacts efficiency however can likewise present security dangers. Moreover, lubrication failures can cause raised friction, resulting in overheating and eventual element failure.
Electrical troubles, commonly coming from loosened links or worn-out wiring, can disrupt machinery functions, leading to substantial manufacturing delays. Finally, software program problems because of incorrect arrangements or outdated programs can prevent the device's operation, demanding prompt treatment. Attending to these usual upkeep issues proactively is essential for making sure optimal efficiency and longevity of packaging machinery.
Preventative Maintenance Approaches
Carrying out preventative upkeep methods is important for maintaining the efficiency and reliability of product packaging devices. These methods include a methodical strategy to maintenance, concentrating on the normal assessment and servicing of equipment to preempt possible failings. By sticking to a scheduled maintenance program, operators can recognize wear and tear on parts prior to informative post they lead to significant malfunctions.
Crucial element of a preventative maintenance method include routine assessments, lubrication, cleansing, and component replacements based on manufacturer referrals. Using checklists can improve this process, making sure that no necessary tasks are forgotten. Furthermore, maintaining precise records of maintenance tasks help in tracking the device's performance in time, assisting in informed decision-making pertaining to future upkeep needs.
Educating staff on the significance of preventative maintenance improves compliance and fosters a society of aggressive treatment. Applying an anticipating maintenance component, making use of data analytics and sensor innovation, can even more optimize equipment performance by predicting failings before they take place.
Troubleshooting Methods
When confronted reference with breakdowns or inadequacies in product packaging machines, employing methodical troubleshooting methods is vital for identifying and resolving concerns swiftly. The very first step in efficient troubleshooting is to establish a clear understanding of the device's functional criteria and performance metrics. This involves examining the machine's specifications, as well as any error codes or alerts shown.
Following, drivers need to perform an aesthetic evaluation, inspecting for obvious indicators of damage, wear, or misalignment. This often consists of analyzing belts, sensing units, and gears to pinpoint possible sources of malfunction. Collecting operational data, such as manufacturing rates and downtime logs, can also offer understandings right into reoccuring concerns.
When possible issues are recognized, making use of a sensible strategy to separate the root cause is important. This might call for screening individual parts or systems in a controlled fashion. Taking part in discussions with operators that interact with the machinery regularly can produce useful comments regarding unusual habits or patterns.
Repair Work and Substitute Ideal Practices
An extensive understanding of repair and substitute ideal methods is important for keeping the durability and efficiency of product packaging machines. Consistently analyzing the condition of equipment parts permits prompt check this treatment, avoiding even more significant concerns that can result in costly downtimes.
When repair work are necessary, it is vital to use OEM (Original Devices Supplier) parts to ensure compatibility and performance. This not just maintains the integrity of the device however also supports guarantee contracts. In addition, it is suggested to keep a supply of essential spare parts to facilitate quick replacements and minimize operational interruptions.
For complex repair work, involving qualified technicians with specialized training in packaging equipment is advised. They have the expertise to detect issues precisely and perform repair work successfully. Recording all fixing activities and parts substitutes is essential for maintaining a thorough upkeep history, which can aid in future troubleshooting.
Last but not least, carrying out a proactive strategy, including regular examinations and predictive upkeep methods, improves the integrity of packaging machines. By sticking to these best methods, organizations can make certain ideal maker performance, lower operational threats, and prolong equipment life-span.
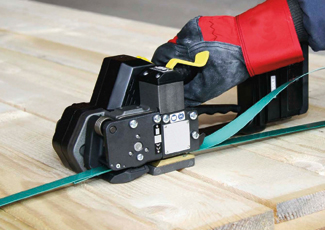
Conclusion
To conclude, an extensive understanding of product packaging maker parts and efficient upkeep strategies is essential for optimal efficiency. Regular examinations and making use of OEM parts can substantially minimize downtime, while a well-documented maintenance background cultivates positive care. Using certified specialists better enhances repair service quality and reliability. By implementing these practices, organizations can ensure the durability and performance of packaging devices, eventually contributing to improved operational productivity and decreased prices.
Efficient maintenance of packaging makers hinges on a complete understanding of their essential elements, including the structure, drive system, and securing systems.Reliable procedure of packaging devices counts greatly on routine maintenance to protect against common concerns that can interrupt production.Executing preventative maintenance methods is critical for maintaining the efficiency and reliability of packaging machines. In addition, keeping precise records of maintenance activities help in tracking the machine's efficiency over time, assisting in notified decision-making concerning future maintenance needs.
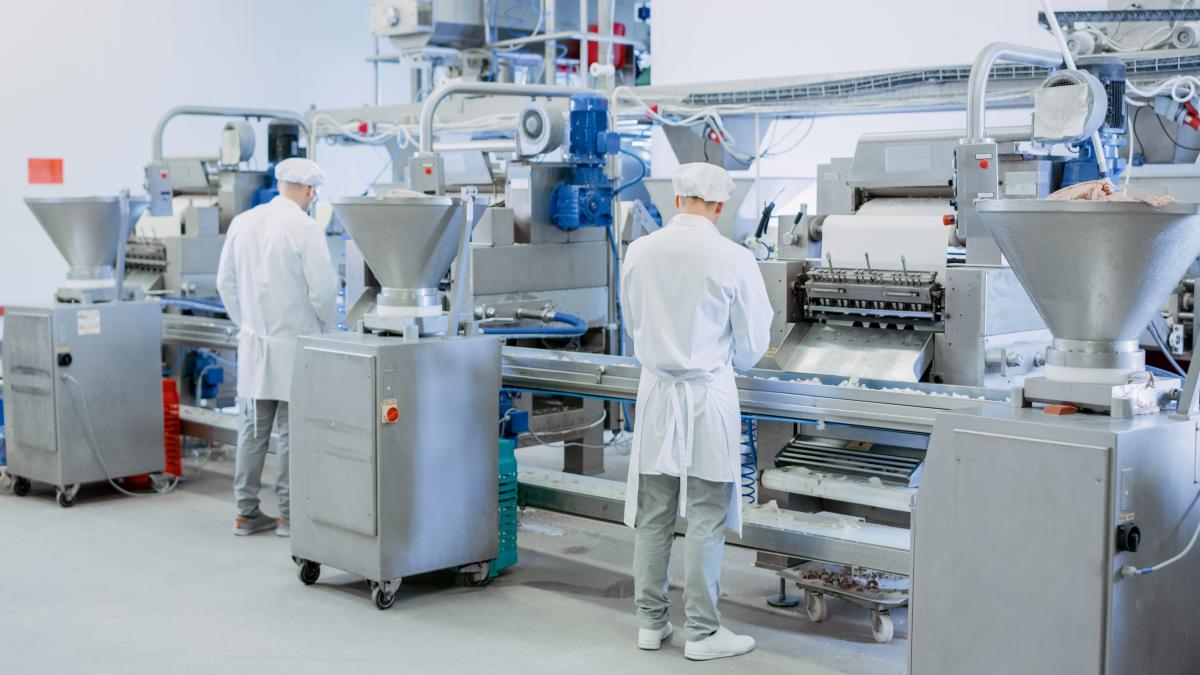
Report this page